Companies are scrambling to turn the greenhouse gas into useful products — but will that slow climate change?
By Mark Peplow, March 29, 2022
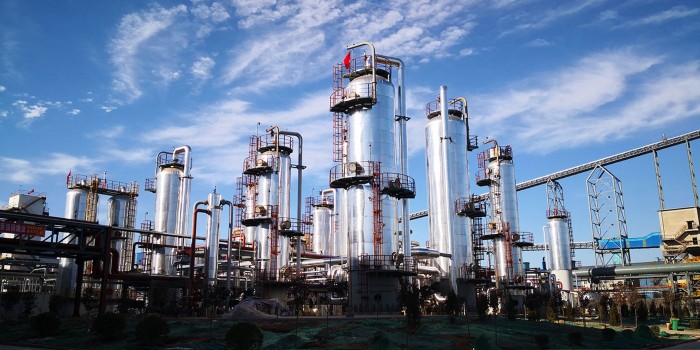
Tongyezhen is a town with coal in its bones. In this part of China’s Henan province, people have been mining coal and smelting metals for millennia. Today, Tongyezhen hosts a sprawling industrial park where huge ovens bake coal and limestone into coke and lime, both key ingredients for producing steel. Unsurprisingly, it is one of the smoggiest places in China.
It might seem an unlikely venue for a clean-technology milestone. But later this year, a chemical plant here is set to become the world’s largest facility for recycling carbon dioxide into fuel. It will combine CO2 from a lime kiln with excess hydrogen and CO2 from a coking furnace to produce methanol, an industrial chemical used for fuel and to make plastics. Carbon Recycling International (CRI), the Reykjavik-based firm behind the operation, says that the Tongyezhen plant will recycle about 160,000 tonnes of CO2 per year — equivalent to the emissions from tens of thousands of cars — that would otherwise go into the atmosphere.
It’s an alluring idea: industrial CO2 emissions are warming the climate, and many countries are working on capturing the gas and storing it underground. But why not recycle it into products that are both virtuous and profitable? As long as the recycling process avoids creating more carbon emissions — by using renewable energy, or excess resources that would otherwise be wasted — it can reduce the CO2 that industry pumps into the atmosphere and lower the demand for fossil fuels used in manufacturing. That’s a double climate win, proponents say.
This kind of recycling (sometimes called upcycling) is an increasingly crowded field, as companies big and small race to market a bewildering array of products made from CO2. Some are boutique items for the climate-conscious shopper — vodka or diamonds, for example — but most are staples of the global economy: fuels, polymers, other chemicals and building materials. More than 80 firms are working on new approaches to using CO2, noted a 2021 report by Lux Research, a market-research company in Boston, Massachusetts. The market for these products is tiny today, amounting to less than US$1 billion — but Lux predicts that it will grow to $70 billion by 2030, and could reach $550 billion by 2040.
This activity is being driven by a fall in the cost of renewable energy, along with rising carbon taxes and other climate incentives that are persuading firms to avoid CO2 emissions. At the same time, chemists have improved the efficiency of the underlying technologies.
But there are tough questions about whether CO2 recycling genuinely benefits the climate. Many of the products made this way only briefly delay carbon’s journey into the atmosphere — fuels are burnt, products made from chemicals degrade and the CO2 consumed during their creation is released again. That will happen at Tongyezhen: much of the methanol produced is destined to be burnt as fuel in China’s growing fleet of methanol-powered vehicles.
Meanwhile, some estimates suggest that the global market for recycled CO2 products is unlikely to lock up more than a few per cent of the CO2 that humans release into the atmosphere by burning fossil fuels, which totalled 36 billion tonnes last year. CRI’s plant, for one, will convert the equivalent of a little over 2 minutes’ worth of annual global CO2emissions. “We can avoid a lot of that, for a lot less money, than we can by turning CO2 into stuff,” says Niall Mac Dowell, an energy-systems engineer at Imperial College London.
“The assumption that we can fix this climate-change problem in an economically attractive and easy way — at best it’s naive, and at worst it’s actively disingenuous,” he says. It’s an argument that’s heating up as CO2 recycling goes mainstream.
Premium product
Using CO2 as a chemical ingredient isn’t a new idea. Roughly 200 million tonnes of CO2 are used in a handful of processes each year, most of it reacted with ammonia to make urea for fertilizers. (Producing ammonia emits extra CO2, and urea’s carbon is quickly released after it is spread on a field, so there are no climate benefits.) The petroleum industry also injects CO2underground to help recover oil, but using that oil can generate more gas than is stored.
What’s changing now is the sheer number of firms that are moving new CO2-recycling methods towards the market and touting their climate benefits. Approaches range from co-opting biological processes to using electrochemical cells or catalysts (see ‘Reusing carbon dioxide’).
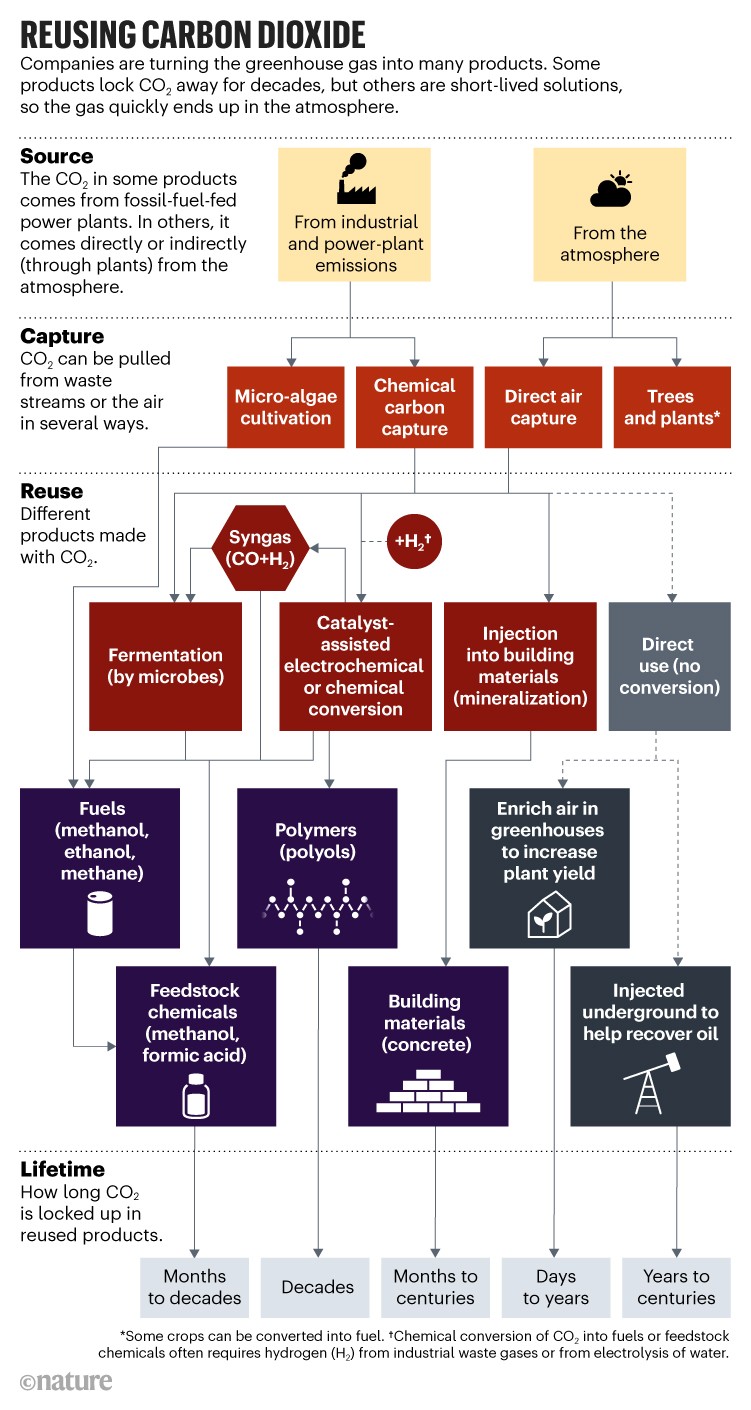
Many of the bigger players use catalysts that help to combine CO2 with hydrogen to make fuels and commodity chemicals. Their main costs revolve around the energy needed to make hydrogen, capture streams of CO2 and break this molecule’s strong carbon–oxygen bonds to forge new molecules. That is why so many early plants are located where there are plentiful streams of high-purity waste CO2, widely available spare hydrogen and heat (which powers the methanol production at Tongyezhen), or low-cost renewable electricity.
CRI, for instance, opened its first CO2-to-methanol plant in 2012, next door to a geothermal power station in Iceland. There, boreholes tap into hot water and steam that come with unwanted CO2. CRI’s plant relies on Iceland’s relatively low-carbon electricity grid to create ‘green’ hydrogen from water by electrolysis. Then the gases are combined, heated, pressurized and passed over a catalyst that eases the breaking of CO2 bonds. Each year, the Iceland plant recycles 5,500 tonnes of CO2.
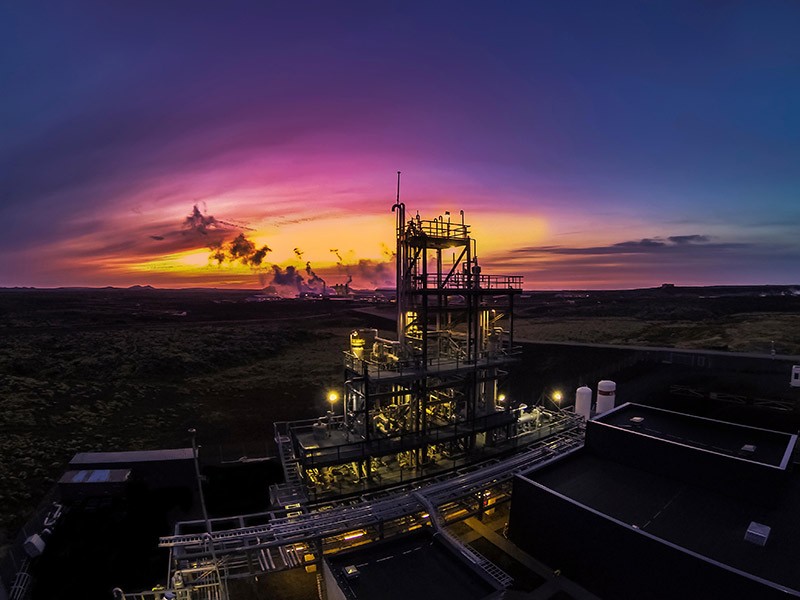
“This is more expensive than producing conventional methanol, there is no doubt about it,” says Emeric Sarron, chief technology officer at CRI, who declines to say how much more expensive. “But companies that need to source renewable fuels are willing to pay a premium for it.” And the firm has customers: as well as the facility in Tongyezhen, CRI is working on other full-size plants in China’s Jiangsu province and in northern Norway. Other consortia projects involving companies in Belgium, Sweden and Denmark will all recycle CO2 to methanol for use as a chemical feedstock and shipping fuel, and aim to start operations between 2023 and 2025.
Electrochemical fuels
Rather than building such large, centralized projects, some start-ups think it will be cheaper and more efficient to convert CO2 inside smaller, modular electrochemical cells. California-based start-up firm Twelve, for instance, aims by the end of this year to have an electrolyser system the size of a shipping container that uses electricity to process more than one tonne of CO2 each day into syngas. This mixture of carbon monoxide and hydrogen is widely used to make other chemicals, including fuels. Twelve plans to offer CO2 conversion as a service to firms wanting to reduce their emissions; it could charge per tonne converted, and sell its end products to cover costs. In July 2021, it raised $57 million in venture-capital funding. “We definitely see ourselves being a player in greenhouse-gas emission reduction,” says Etosha Cave, the company’s co-founder and chief scientific officer.
Syngas is conventionally made by an energy-intensive process that crushes methane and water together at high temperatures and pressures. Twelve, by contrast, uses a modified commercial electrolyser, which normally splits water into hydrogen and oxygen. Adding a metal catalyst to one of the device’s electrodes (the cathode) enables it to simultaneously convert CO2 into CO, so that the system produces syngas at room temperature. Twelve aims to use renewable electricity sources to run these CO2-recycling units.
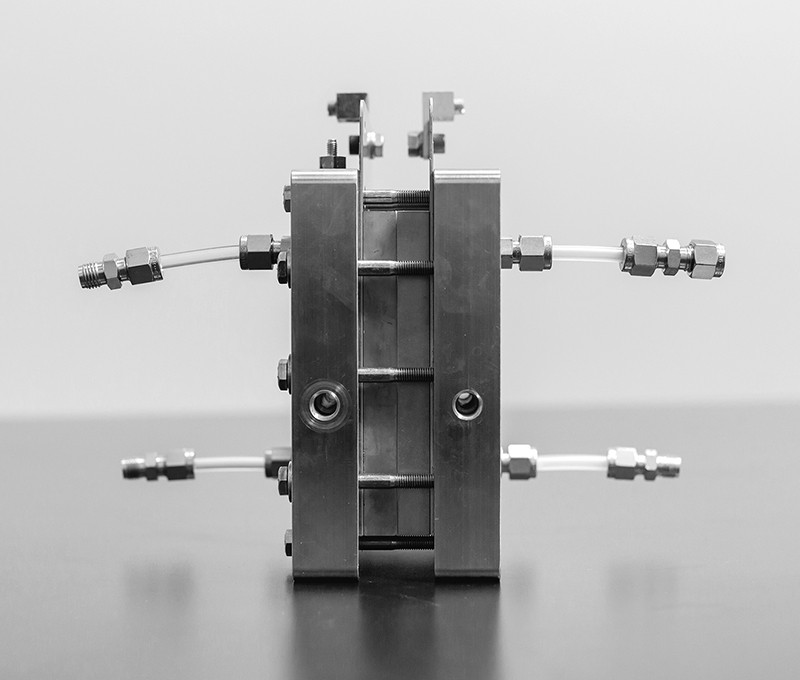
Academic chemists have pressed the case for electrochemical recycling by making significant improvements to cathode catalysts. A key metric known as Faradaic efficiency — the proportion of electrons that go into producing CO rather than unwanted by-products — is now more than 90% in some cases1. Chemists are also making headway on another front — improving the ability of catalysts to support a high electric-current density. This allows a given area of electrode to convert more CO2 molecules. Nevertheless, many catalysts struggle to work for more than a few hundred hours before they start to degrade, says Jan Vaes, programme manager for sustainable chemistry at the Flemish Institute for Technological Research (VITO) near Antwerp, Belgium.
Electrochemists aren’t only targeting syngas. Avantium, a renewables chemical company in Amsterdam, is using improved catalysts2 to make formic acid, which can be converted into more-valuable chemicals. It is currently testing an electrochemical reactor at a fossil-fuel power plant in Germany.
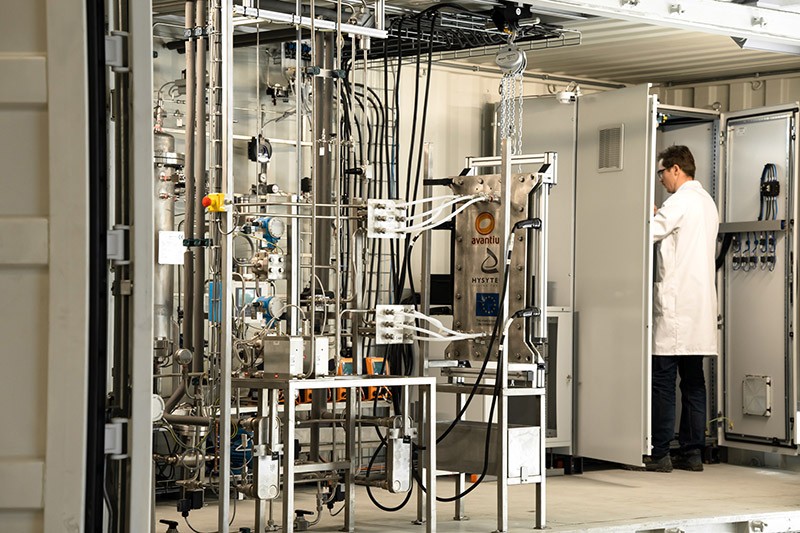
And some chemists are hoping to make more complex carbon molecules that could command higher prices. Larger molecules can be more troublesome to make this way — with more chemical bonds, there are more opportunities for electrons to be diverted into side products, reducing efficiency — but progress is being made. This year, for instance, electrical engineer and materials scientist Edward Sargent at the University of Toronto in Canada and his team unveiled an electrochemical system that converts CO2 and water into ethylene oxide, which is widely used to make polymers. The team’s catalyst achieved a record Faradaic efficiency of 35% for the conversion3.
Life-cycle arguments
Whether products recycled from industrial CO2 emissions actually protect the climate is unclear — because the CO2 they capture will still be released into the atmosphere if the molecules are burnt or broken down. Drawing CO2 directly from the atmosphere could have clearer climate benefits, but capturing the gas from air is extremely expensive, as are products made that way.
Proponents argue that recycling industrial CO2 into chemicals can reduce emissions in another way — by avoiding some fossil-fuel-based production. “Our process helps keep fossil fuels in the ground by tapping into existing streams of CO2,” a spokesperson for Twelve told Nature.
The stringent way to examine this is through a life-cycle analysis (LCA) — a detailed accounting of the carbon involved in making and using a product, from the origins of its CO2to its final fate. Many CO2-recycling firms say they have done these audits, but don’t publish them because they contain proprietary information.Climate pledges from top companies crumble under scrutiny
One firm that has released LCAs is LanzaTech, headquartered in Skokie, Illinois. The company uses bioreactors filled with Clostridium autoethanogenum bacteria to ferment industrial CO2, CO and hydrogen waste emissions into ethanol. Its chief executive, Jennifer Holmgren, notes that this kind of bioconversion can handle messy waste-gas streams, such as those from municipal waste gasifiers, better than chemical processes do. The firm’s reactor at a Shougang Group steel plant near Tianjin in China has been producing ethanol since 2018. A second plant began operating at a Chinese alloy plant last year, and commercial plants in Belgium and India are expected to come online by the end of this year.
On 8 March, LanzaTech announced that it would become publicly listed, a move that values the company at $1.8 billion. This year, it reported that with genetic modifications, its bacteria could make larger molecules such as acetone and isopropanol, too4. Conventional production of acetone and isopropanol generates copious CO2 emissions. By contrast, LanzaTech’s LCA suggests that its route is carbon-negative — consuming much more carbon than it emits4. But this analysis did not include what would happen to the CO2 when the products were used.
Holmgren thinks that CO2-based products will save on emissions anyway, by displacing their conventionally made equivalents. But she concedes that it is hard to be certain this is true — CO2-based products might simply add to the growing global consumption of fuels and other chemicals, rather than displace incumbent production. It’s also tricky to pin down direct evidence for displacement in such a nascent market, adds Sarron.
“The problem is that people use displacement with the idea that the market will do it, somewhere around the globe,” says Andrea Ramírez Ramírez, who studies low-carbon systems and technologies at Delft University of Technology in the Netherlands. “But how do you monitor displacement? That’s very, very difficult.”
A greater availability of supposedly guilt-free CO2-derived products might also lead to increased consumption of those resources, she adds. Anyone who is trying to limit their international flights, for instance, might fly more often if their airline boasts of its climate-friendly fuel. This ‘rebound effect’ has been observed for some energy-efficiency measures, Ramírez Ramírez says, although it hasn’t been studied for CO2-based goods.
In her view, negative emissions5, such as those claimed by LanzaTech, “should mean real CO2removal from the atmosphere, that you can actually measure physically”.
Locking carbon down
To maximize climate benefits, it makes more sense to lock recycled CO2 into products that last for decades. That’s where polymers come in. “You’re making products like insulation foam, mattresses, soft furnishings, that have quite a long lifetime,” says Charlotte Williams, a chemist at the University of Oxford, UK.
Williams develops catalysts that can incorporate CO2 into polyols, which are used to make polyurethane foams. Polyols are usually made from expensive chemicals called epoxides, but her catalysts help CO2 to take the place of some of these in the polymer chain. This traps CO2and reduces the consumption of epoxides — which themselves have a big carbon footprint.
Concrete needs to lose its colossal carbon footprint
Williams has founded a spin-off company, Econic Technologies. In September 2021, it signed a deal to build a pilot plant in India, and then retrofit an existing plant to incorporate waste CO2 into polyols. Other companies are seasoning polymers with CO2 in similar ways.
Despite this progress, projections suggest that using CO2 as a polymer ingredient would lock up only around 10 million to 50 million tonnes of CO2 per year by 20506. So, is it really worth it? “I think it’s the wrong way of looking at the problem,” Williams says. “We have to make massive cuts in CO2 emissions across the board, but we also have to invest in some technologies that can directly use it.”
The biggest opportunity to incorporate CO2 into products lies in concrete and other building materials, says Runeel Daliah, a senior analyst at Lux Research, who is based in Amsterdam. The technology is proven and scalable, and could feed an enormous global demand for concrete, giving it the potential to dominate the CO2-conversion market. “Concrete is really the only one where you have permanent sequestration of CO2 in the product,” Daliah says.
One of the leaders in this sector is Canadian company CarbonCure in Halifax. Founded in 2012, it pumps waste CO2 into fresh concrete to form nanoparticles of calcium carbonate. This improves the compressive strength of the concrete, so that less cement is needed7. Because cement-making accounts for most of concrete’s carbon emissions, the company says this could reduce the carbon footprint of every tonne of concrete by around 5% (or 6 kilograms of CO2).
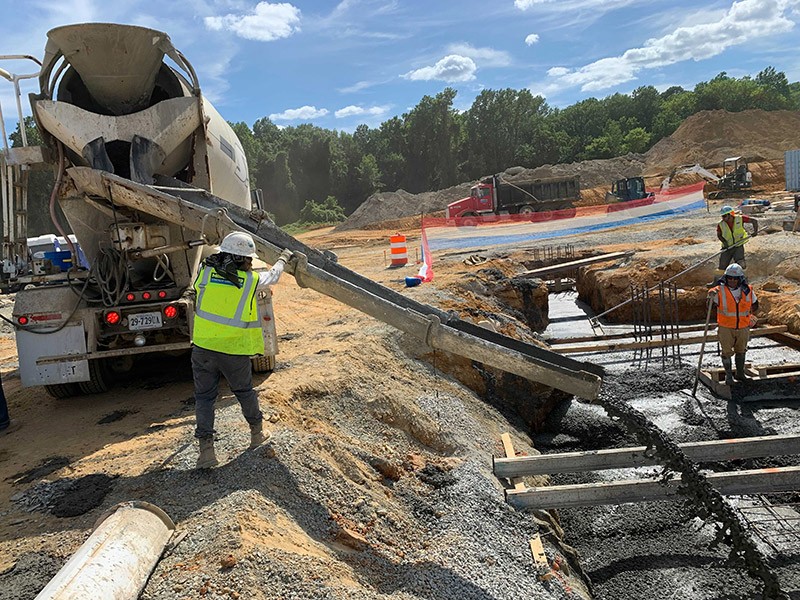
The company has installed more than 550 of its CO2 injection units at concrete plants around the world, most of them in North America, which has avoided and mineralized 150,000 tonnes of CO2 emissions so far. But with some 100,000 plants worldwide churning out roughly 33 billion tonnes of concrete per year, “we’re really just scratching the surface”, says Jennifer Wagner, CarbonCure’s president.
Ramírez Ramírez says that converting CO2 into minerals offers a much clearer climate benefit than converting it into fuels. “In the life-cycle analysis, you can see the benefits are much larger, and I think much more robust.”
Carbon-removal incentives
When it comes to making fuels and other chemicals, most CO2-derived products are currently more expensive than their conventional rivals, says Josh Schaidle, who led an analysis by the US National Renewable Energy Laboratory in Golden, Colorado, of 11 products made by CO2conversion8. Yet they could still have a strong business case, if they can take advantage of low-cost renewable electricity, as well as the tax breaks, subsidies and quotas that aim to wean the world off fossil resources.
In the European Union, for instance, a broad package of policy incentives under the banner of the European Green Deal aims to make the bloc climate neutral by 2050. Pending legislation specifies quotas for the use of CO2-derived fuels in aviation. There will be reduced taxes on CO2-based fuels, and the promise of plenty of innovation funding to help technologies to market.
Microsoft’s million-tonne CO2-removal purchase — lessons for net zero
In the United States, some companies say that a tax credit called 45Q is helping to encourage CO2 conversion. It pays industries $50 for every tonne of CO2 they store permanently underground, or $35 if they put the CO2 to use. In China, there has been relatively little commercial activity in developing CO2-conversion technologies9. But in 2021, key players in China’s gigantic chemicals industry pledged to invest in CO2-based chemical production, a move that could win financial support through the country’s carbon-trading market, which launched last year.
The success of the CO2-conversion businesses, however, could rest on LCAs and other measurements of carbon flows. The European Commission, for example, is developing a carbon-removal certification mechanism to provide a more rigorous framework for verifying whether a process is genuinely carbon negative.
So far, LCAs offer a rather downbeat assessment of most CO2-conversion strategies. In a report10 published in February, environmental scientist Kiane de Kleijne at Radboud University in Nijmegen, the Netherlands, and her colleagues scoured dozens of published LCAs to compare CO2 conversion routes with conventional ways of making the same products. Then the researchers compared CO2 savings from the recycling processes with the 2015 Paris agreement targets of halving global CO2 emissions by 2030, and of achieving net zero emissions by 2050. “We found that very few of those routes are able to meet the criteria for Paris compatibility,” says de Kleijne. Routes that made the grade did so by storing CO2permanently — mixing the gas with slag from steel mills to make construction blocks, for example.
Climate-focused academics conducting LCAs often note that geological storage of CO2 is better than conversion because it offers much greater reductions in emissions. That might be true, but it ignores a brutal economic reality, says Sarron. “Putting carbon back into the ground is expensive, and is not happening at a meaningful scale. The alternative to what we are doing today is not storage, it’s emission to the atmosphere.”
And if the global economy does eventually end its reliance on coal, oil and gas, industries of the future might need these CO2-conversion processes to produce the polymers and other chemicals we depend on.
De Kleijne says that all too often, the academics performing LCAs and companies developing CO2-conversion systems end up talking past each other on these issues.
But there is at least one point of broad agreement: that CO2 recycling technologies should eventually draw as much of their feedstock as possible from the atmosphere, rather than from waste industrial gases. A project called Norsk e-Fuel in Oslo is taking a step in that direction with a pilot plant in Herøya, Norway, which aims to start turning CO2-derived syngas into jet fuel. Some of the CO2 will come directly from the air, snared by carbon-capture technology developed by Climeworks, a company that was spun off from the Swiss Federal Institute of Technology in Zurich in 2009.
That technology is now in operation at Climeworks’s first large-scale direct air-capture plant, which opened in September 2021 in Hellisheidi, Iceland. It will capture 4,000 tonnes of CO2 a year to be pumped underground. It costs $600–800 to sequester one tonne of CO2 in this way — hardly cheap — but the company says it can slash that to one-tenth of the cost as it scales up.
Even if there are limited climate benefits from converting today’s fossil CO2 emissions into products, some companies argue that it’s important to develop the technology so that it is ready to feed off CO2 from the air once direct air-capture technology matures. “I do think it’s a valid argument,” says Ramírez Ramírez. “But we need to be careful that it is part of a transition, that we eventually replace the fossil carbon with sustainable sources.”
Nature 603, 780-783 (2022)
To read the article in Nature click here.